Author:
Brain Teague, MicroCare Product
Manager
Industry : Fiber Optics
Published : Cabling Installation & Maintenance
Improperly cleaned fiber end-faces have operational and financial implications, but can be avoided.
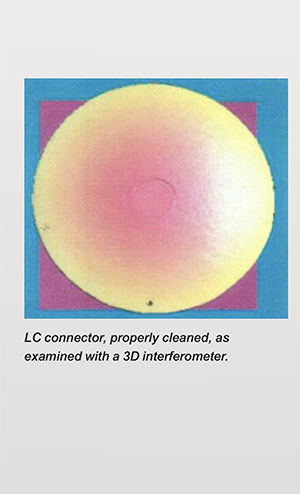
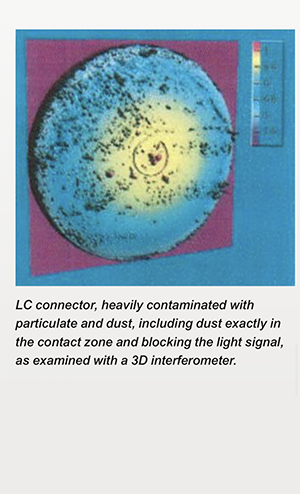
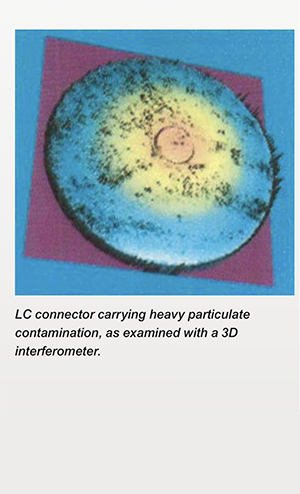
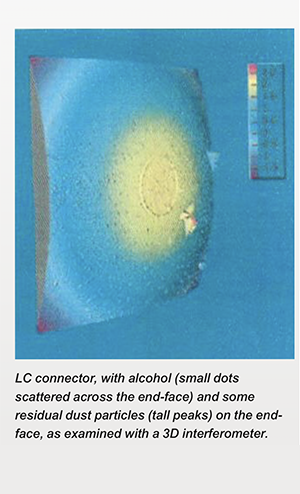
Every cable assembly manufacturer strives to produce pristine ferrule end-faces with zero defects. In the real world, this lofty goal is impossible to achieve. Even the best cable assembly manufacturers have an occasional scratch or pit on the ferrule end-face.
The purpose of this article is to review the current operational and financial implications of improper cleaning of end-faces, and to suggest improved techniques that will reduce operating costs and improve network reliability.
The Industry Standard
As a matter of background, the International Electrotechnical Commission (IEC) published the fiber end-face specification 61300-3-35. This standard was developed to guide the fiber-optic industry in determining what kind of defects could be on the ferrule end-face with no negative performance impact.
Digital ferrule scopes are commonly used in production and by field installers to inspect ferrule surface quality and comply with this specification. Most digital scopes employ automated, software-driven algorithms to accurately compute the
size, area, and location of end-face defects. This is an important advancement for the industry; every installer should have this type of gear available to them in the field.
The reason for this concern is that the location of defects relative to the center of the fiber core — the contact zone — is the critical measurement. A 1-pm or 2-pm length can be the difference between having an end-face that meets or fails the 61300-3-35 specifications. Even the most experienced operator cannot visually determine if a scratch is 5 pm or 6 pm in length. The use of a digital ferrule scope with automated analysis software set to the IEC 61300-3-35 standard eliminates human error in determining if a defect will negatively impact network performance.
Field installers have limited options for addressing permanent defects like pits and scratches on the ferrule end-face. The vast majority of cable assembly manufacturers perform 100-percent optical testing, so it would be a rare occurrence to get a fiber cable assembly shipped from the factory out of spec.
Contamination Types
The more common end-face defect that field installers encounter is generally termed “debris.” Debris is dust, lint, plastic or ceramic particulate, fingerprint oils or a host of other contamination. The industry’s best practice is to remove all debris from both connector end-faces using optical-grade cleaning materials before mating the connectors. LC connector, properly cleaned, as examined with a 3D interferometer.
Inspect, Clean, Inspect
It is vitally important to inspect each end-face after cleaning and before mating to ensure the debris is removed. At a minimum, failure to remove the debris will cause cross-contamination of the two ferrule end-faces, disrupting the optical signal path. Particulate debris in the contact zone frequently causes scratches and pits on both connector end-faces. This is the reason Section 5.3 of IEC 61300-3-35 advises installers to inspect the connector end-face, clean the end-face if necessary to remove contamination, and re-inspect the ferrule. The total inspection process, using a digital ferrule scope, takes less than five seconds for an accurate analysis. Importantly, most modern digital scopes also capture an image of the ferrule end-face. This helps to document the condition of the end-face and ensures the performance of the network.
Static Charge Problems
Dry particulate has a very sly manner of moving onto fiber end-faces and causing network problems. The symptoms of the problem are perplexing. For example, an operator cleans and inspects an end-face, and sees a pristine result. Then, the operator returns at a later date and finds troublesome dust particles on the end-face. How can this happen?
The problem is the process, not the particulate. Dry-wipe cleaning is a common process used by well-intentioned installers. However, any time two different materials rub together there is a transfer of surface electrons that creates a static charge. The technical term for this event is “triboelectric charging.” The contact friction from the wiping process creates a static charge on surfaces of both the connector and the wipe itself.
Dielectric materials like ceramic ferrules and composite MT ferrules are insulators, not conductors, and they will store the static charge. The voltage remains trapped indefinitely until a conductive path is created. Any debris residing inside the connector housing quickly becomes attracted to the ferrule end-face and tightly bonds to that surface by what is known as electrostatic attraction (ESA).
Sources of Static
Static, as all forms of electricity, follows the path of lowest resistance. Static charge on an end-face builds up to the highest levels to the apex of the end-face. A common cause of static charge is using a dry wipe or swab to clean connectors in low-humidity environments. This causes particles attracted to the static to migrate toward the contact region of the ferule, where it causes the most problems. Common sources of static charge caused by contact friction in optical networks include the following.
- Dry-wipe cleaning
- Insertion of inspection scopes and test gear into adapters
- Connector mating
- Equipment cooling fans and fans in the HVAC system
Solving the Static Problem
Static charges on the end-face attracts and holds particulate debris for days and even months. The debris remains bonded to the end-face until the static charge finds a conductive path for it to dissipate. The introduction of a cleaning fluid creates that conductive path, making it easy to physically wipe the debris away.
The most effective cleaning process to solve this problem is using an optical grade cleaning fluid. The liquid temporarily creates the conductive medium for the static to dissipate.
Cleaning at What Cost?
Cost implications of not cleaning contaminated end-faces such as those described above can be very costly. Dirty connectors will slow data speeds and, in the worst case, bring a fiber network down. What will this cost?
The average cost of network downtime is approximately $8,000 per minute. Industries suffering the highest downtime cost included hospitality, public sector, transportation, and media organizations. Installation companies are investing large amounts of capital in the latest network testing gear and personnel training to meet project requirements and customer expectations. But for the networks to operate at their designed reliability, companies must use the proper cleaning tools.
Here’s another way to look at it: Labor costs account for 60 to 80 percent of fiber deployment expenses. The cost to roll a truck and crew back to a worksite to repair a network failure is typically around $250 to $500 per incident. Unfortunately, after spending huge sums on test equipment and training, many companies suddenly become overly frugal and choose the cheapest options instead of the most effective options when selecting the connector cleaning consumables to be used on the work site.
Invest in a Quality Cleaning Fluid
Isopropyl alcohol (IPA) and paper-based tissues are the lowest-cost options and most common cleaning consumables. Both are poor choices.
As a cleaning fluid, IPA has a major deficiency. It is hygroscopic. Meaning it attracts water molecules from the air even at low relative humidity.
IPA packaged in containers that are not hermetically sealed can easily become contaminated by atmospheric moisture as well as the dust particles that float in the air. Dust particles floating in the air bond with water molecules and then absorbed into the IPA. After two or three days, the 99-percent IPA that was poured into the container is diluted with floater particles.
Alcohol is also highly flammable and has a high vapor pressure that makes it dangerous to use in areas where there are flames or sparks. Most alcohol-based cleaning solvents also are regulated hazardous materials and cannot easily be shipped by air.
Replacing IPA with a precision cleaning fluid engineered for optical device cleaning is a better option for cleaning fibers and connector end-faces. Unlike IPA, high- quality fiber-optic cleaning fluids clean better, dry quickly, and do not leave a residue on the end-face. To further minimize the risk of contamination, use a cleaning fluids packaged in a hermetically sealed, nonrefillable container.
Cleaning fluids and packaging developed and tested specifically for cleaning fiber optics produce the best results.
Replace the Paper Wipes
Paper-based tissue wipes are cheap, but cause more problems than they solve. They have a low shearing strength, causing the fibers to separate easily as the operator wipes the ferrule end-face. This deposits debris on the end-face.
Some installers use pre-saturated alcohol wipes to clean fiber end-faces and fibers for splicing. Pre-saturated wipes frequently become cross-contaminated. Plus, the cleaning fluid causes the packaging to break down over time. Temperature cycling accelerates degradation of the packaging material, which begins to leech into the cleaning fluid and contaminate the wipe.
Make sure to only use optical-grade, lint-free wipes that have high absorbency and high shearing strength. Reusing wipes and cleaning sticks will eventually cause problems related to cross-contamination.
Avoid Water
Avoid using aqueous (water-based) cleaners. Aqueous cleaners are weak cleaners, slow to dry, and can leave moisture and streaks on the end-face. Aqueous-based solutions are also susceptible to freezing in cold climates.
Make Better Cleaning Choices
Famed basketball coach John Wooden used to ask his players at the University of California Los Angeles, “If you don’t have time to do it right the first time, when are you going to have time to do it right?” Therefore, my final recommendation
to installers is this. Pick the right cleaning materials made for cleaning optical connectors, and do it right the first time. Failure to heed this advice will cost you long term in callbacks, network downtime, and frustrated customers.
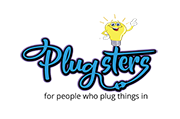